Background
Siemens, a leading healthcare company, partnered with Solsta to address their needs for sourcing components for a spectrometer subassembly used in one of their urinalysis instruments. Solsta not only provided Siemens with the necessary components such as LEDs and CCDs but also facilitated an introduction to a subassembly manufacturer. Solsta managed the supply chain to deliver the completed subassembly to Siemens. However, when the subassembly manufacturer later closed down its production facility, it posed a threat to Siemens’ urinalysis instrument production. Solsta proactively stepped in to remedy the situation by transferring the production of the subassembly in-house to their facility in Weymouth.
Solution

Solsta effectively completed the transfer of production for the urinalysis instrument subassembly, ensuring Siemens’ continued manufacturing capabilities. During the transfer process, Solsta implemented several improvements to enhance the production process. They automated the die stamping and wire bonding processes, resulting in improved reliability and accuracy during assembly. Additionally, Solsta enhanced the qualification and test procedures, further reducing the possibility of errors or failures in the manufacturing process.
Benefits
Continued Production: By swiftly transferring the production of the subassembly to their own facility in Weymouth, Solsta ensured uninterrupted manufacturing for Siemens’ urinalysis instrument. This seamless transition prevented any disruption in the supply chain and allowed Siemens to continue meeting the demands of their customers.
Improved Production Process
Solsta’s automation of the die stamping and wire bonding processes led to enhanced reliability and accuracy during assembly. The automation reduced the potential for human error, leading to improved product quality and consistency. These process improvements contributed to increased efficiency and reliability for Siemens.
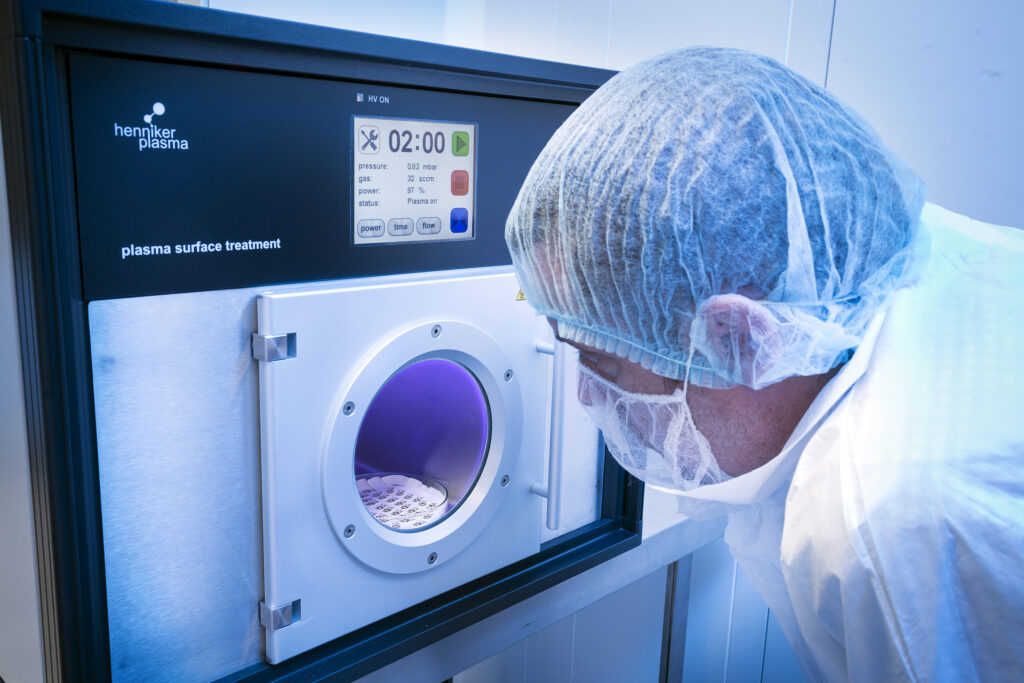
Enhanced Qualification and Testing
Solsta’s improvements to the qualification and test procedures further minimised the possibility of errors or failures during the manufacturing process. By implementing rigorous testing protocols, they ensured that the subassembly met the required standards and specifications, increasing overall product reliability.
ISO 13485 Certification
Solsta’s quality operating procedure certification for compliance with the ISO 13485 medical standard demonstrates their commitment to manufacturing high-quality medical devices. This certification assures Siemens and their customers of Solsta’s adherence to stringent quality management practices, further strengthening the partnership between the two companies.
Continued Partnership
With the successful transfer of production and their recent ISO 13485 certification, Solsta has strengthened its value as a supplier to Siemens’ Healthineers diagnostic instrumentation range. The ongoing partnership between the two companies allows for collaboration on new projects and the potential for further advancements in diagnostic instrumentation.
Conclusion
Solsta’s collaboration with Siemens in sourcing components and managing the supply chain for the urinalysis instrument subassembly exemplifies their ability to provide comprehensive solutions to complex challenges. By swiftly transferring production in-house and implementing process improvements, Solsta ensured the continuity of Siemens’ urinalysis instrument manufacturing. The ISO 13485 certification and ongoing partnership further solidify Solsta’s position as a trusted supplier to Siemens’ Healthineers diagnostic instrumentation range.
Contact Solsta today to explore how they can assist you in optimising your supply chain and enhancing your design and production processes for medical devices and instrumentation.