Background
GSK, a prominent pharmaceutical company, sought to enhance the speed and yield of drug production through photocatalysis. Previous approaches using broad spectrum fluorescent lighting had yielded inconsistent results, and so GSK approached Solsta with a request to design an instrument capable of testing the optimal wavelength and power level of LED illumination for specific reactions in drug production.
Challenges
The challenges for Solsta were to develop an instrument that could be used to determine the optimum wavelength and power level of LEDs for photocatalysis. The instrument should accommodate cassettes of 48 LEDs at single wavelengths, allowing for concurrent use of 48 sample vials. It should also enable the selection of specific power settings with continuous adjustment, support constant or pulsed light operation with a variable duty cycle, offer a range of wavelengths for direct comparison, and be compatible with both batch chemistry vials and flow chemistry plates.
Solution
Working closely with the scientists at GSK, Solsta successfully designed an instrument that addressed the requirements for optimising photocatalysis in drug production. The instrument features cassettes with 48 LEDs at single wavelengths assigned by GSK, enabling controlled test parameters. The optical power can be set to a specific level with continuous adjustment, and the LEDs can be operated in either constant or pulsed mode, offering flexibility in experimentation. An additional cassette using 24 LEDs provides balanced optical output power across six different wavelengths for direct comparison of results. The instrument is designed to accept housings for batch chemistry vials or a flow chemistry plate, accommodating different experimental setups.
Benefits
Maximised Drug Yield: The instrument designed by Solsta enables GSK to determine the optimum optical power and wavelength for photocatalysis of different chemistries, leading to increased drug yield while minimising byproduct generation. This optimisation by experimentation allows GSK to confidently invest in scaled up production equipment, knowing that the efficiency and effectiveness of the drug production processes will be optimised.
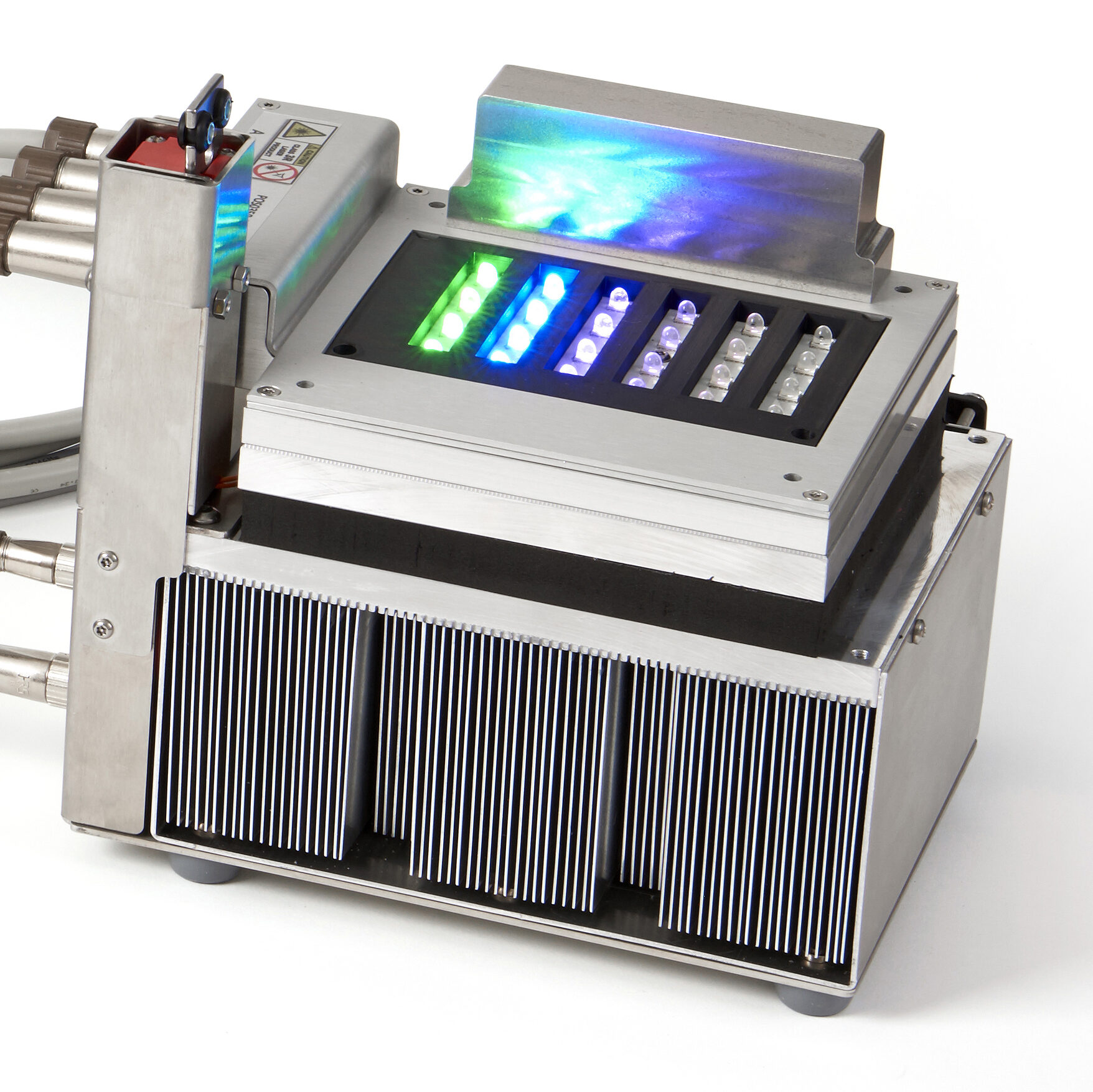
Conclusion
In partnership with GSK, Solsta successfully designed an instrument that addresses the challenges of optimising photocatalysis for drug production. The instrument’s ability to facilitate determination of the optimal wavelength and power for drug production, along with its configuration flexibility for different experimental setups, empowers GSK to enhance drug yield and efficiency while minimising byproduct generation. Solsta’s collaboration with GSK showcases their expertise in developing customised instruments for pharmaceutical applications.
Contact Solsta today to explore how they can assist you in designing and manufacturing innovative instruments and subsystems to advance scientific research and development processes.