When you think of a warehouse, cutting edge technology may not be the first thing that comes to mind. However many warehouses today are at the forefront of industry 4.0 – whether that is in relation to the Internet of Things (IoT), machine learning (ML), artificial intelligence (AI), or perhaps more importantly, laser-guided driverless vehicles. Thanks to these developments, countless human hours are saved and the scope for potential error is minimised.
Guidance Automation’s technology has been leveraged by state-of-the-art driverless vehicles for indoor warehouse usage for over three decades. The company approached Solsta to help develop a next generation laser guidance system to cut costs and improve resilience.
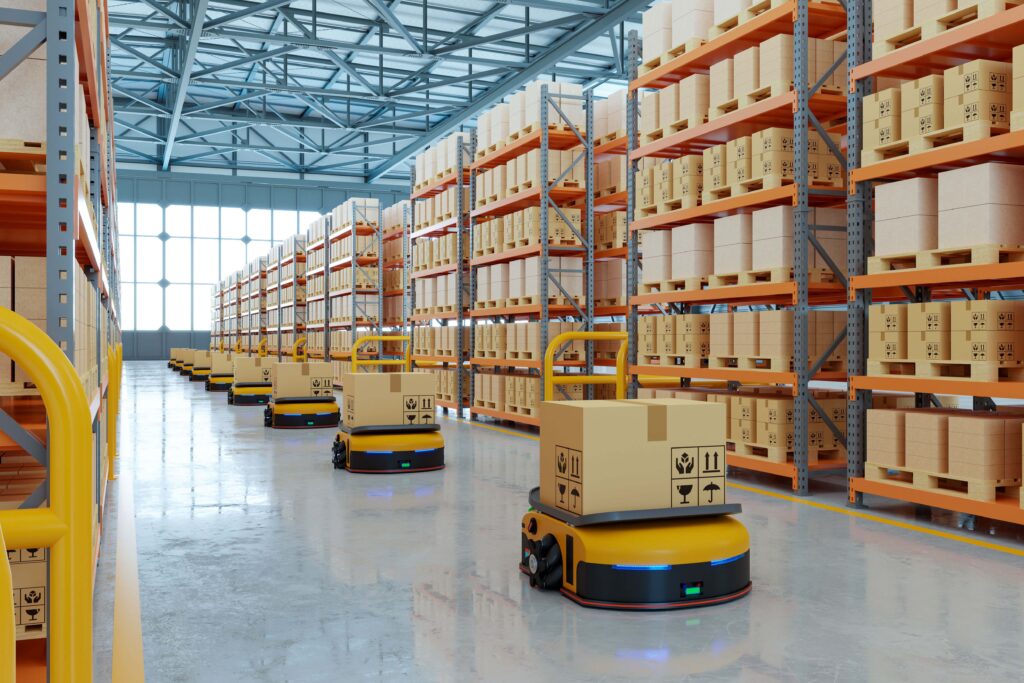
Improving product resilience
Traditionally, robots have operated on the shop floor using a rotating LiDAR system that sent out a continuous beam – searching for retroreflector target surfaces in known locations, reflecting the signal back towards its source. Triangulation made it possible to identify the robot’s position relative to the floor plan. However, not only did this require a shop visit by the vendor or a surveyor to install reflectors (both initially and whenever the layout was changed), but the robot also needed a second, short-range laser scanner (as a safety device) to detect potential people or objects that could be moving and cause an obstruction.
Today, these machines do not need mapped reflectors as the robots can self-map the warehouse without them. Guidance Automation wanted to combine this floorplan-agnostic guidance system laser with a laser capable of detecting all natural features. This would cut costs, as no surveyor would need to visit the site. It would also improve product resilience, and fully futureproof the company against threats from the competition.
To ensure technology met the vision, they turned to a long-standing relationship with a trusted partner – Solsta . Guidance Automation had the idea, but lacked the internal resources and sector knowledge to take this optical system concept to the next step.
Lack of resources
As Dr. Paul Rivers, Managing Director at Guidance Automation, commented; “We’ve always been a pioneering company in the development of warehouse robotics and the laser based ‘indoor GPS’ systems that they need to operate safely and effectively. However, time and time again, our position in the market came up against the limits of technology; the laser optics and internal resources to develop them were simply unavailable.”
“We didn’t have the research and development team to take this challenge on alone, but Solsta did, thanks to their international reach and deep technical expertise. Luckily, we could work with Solsta ’s permanent team of optical experts,” he continues. “Collaboration isn’t just about knowledge sharing – it is also the shared, physical, and human capital it allows access to. Without Solsta , we would have had to hire temporary staff to tackle the project. Not only was this an ethical concern, as no one wants to hire and fire staff, but it was also an operational risk; without permanent employment, talent would be hard to find and even harder to keep on board if they were offered a different and more permanent role.”
A view from the outside
This external influence was not just beneficial from an operational point of view, but also from a technical one. A ‘view from the outside’ was essential for seeing the current innovations and future potential in a new light. This ensured the project was seen as a technical challenge to overcome, rather than just more work for a small and resource-stretched team to do. Like in any context, a fresh pair of eyes can often see new and novel solutions to any issues others may have missed.
According to Dr. Rivers; “Our work with Solsta meant that our latest product is fully futureproofed and entirely innovative – and all the while reducing internal overheads, maximising the project’s resilience against a fast-moving market, and improving reliable access to much-needed talent.”
Next generation of laser guidance system
The Special Projects Group at Solsta stepped in to design this next generation of laser guidance system, developing a range finder based on a pulsed laser and an avalanche photodiode (APD). The pulsed laser allows a higher-intensity signal that remains within the limits of safe average power. Using an APD instead of a standard photodiode enables detection of a weaker return signal. It is the combination of these innovations, alongside clever software to pick the signal out of background noise, which gives the sensitivity needed to determine the robot’s position against both a floorplan and those moving within it.
Barney Mitchell, Manager of Solsta’s Special Projects Group, explains; “The module that my team has developed continuously measures the angular position of the laser. Combining this information with the pulse time of flight to natural targets allows the module to infer distance and speed, and by triangulation with other targets, absolute position on the factory floor.”
Prototypes have demonstrated the ability to detect objects at over 50m away, which is expected to extend further still in factory conditions – thus allowing the robot to move at higher speeds safely. It will also enable outdoor navigation, even in direct sunlight, so that robots can travel between warehouses. Mitchell added; “Thanks to our fantastic supplier portfolio on the distribution side of our business, the material costs for the unit are kept highly competitive. Combined with our DFM approach to design which allows quick and efficient assembly at our Weymouth manufacturing plant, this innovative solution is expected to come at a per-unit price which is lower than competing off-the-shelf solutions with lesser capabilities.”
Contact us to find out more about how Solsta can help you.
This case study was first published in full by EPD&T – November 2023